Fundição de molde de conchaé um processo no qual a areia misturada com uma resina termofixa entra em contato com uma placa metálica aquecida, de modo que uma fina e forte casca de molde é formada ao redor do padrão.Em seguida, a casca é removida do padrão e a capa e o arrasto são removidos juntos e mantidos em um frasco com o material de apoio necessário e o metal fundido é derramado no molde.
Geralmente, areia seca e fina (90 a 140 GFN) completamente livre de argila é usada para preparar a areia de moldagem de concha.A granulometria a ser escolhida depende do acabamento superficial desejado na peça fundida.Um tamanho de grão muito fino requer grande quantidade de resina, o que torna o molde caro.
As resinas sintéticas utilizadas na moldagem de conchas são essencialmente resinas termofixas, que endurecem irreversivelmente pelo calor.As resinas mais utilizadas são as resinas de fenol formaldeído.Combinados com areia, eles têm uma resistência muito alta e resistência ao calor.As resinas fenólicas utilizadas na moldagem de conchas geralmente são do tipo dois estágios, ou seja, a resina possui excesso de fenol e age como um material termoplástico.Durante o revestimento com a areia a resina é combinada com um catalisador como hexa metileno tetramina (hexa) em uma proporção de cerca de 14 a 16% para desenvolver as características de termofixação.A temperatura de cura para estes seria em torno de 150 C e o tempo necessário seria de 50 a 60 segundos.
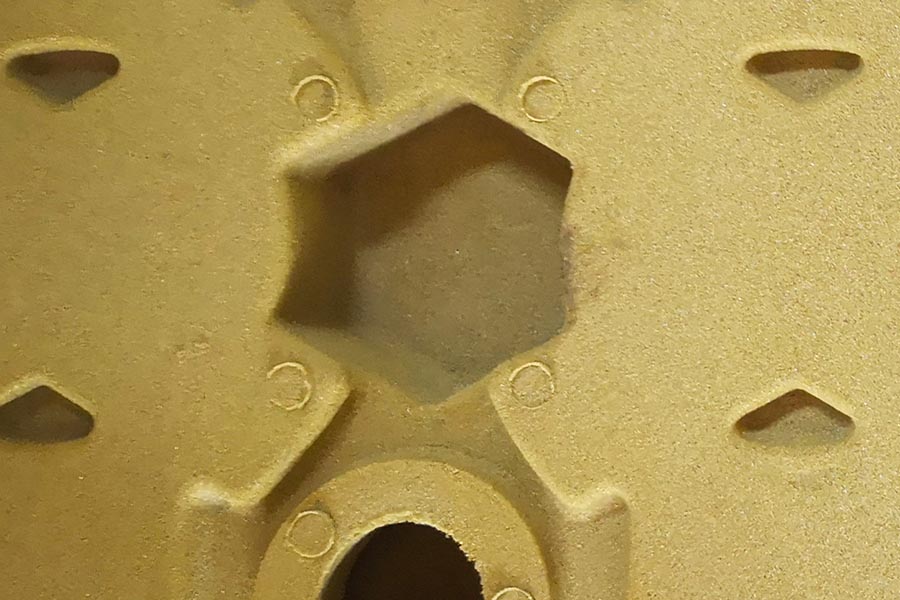
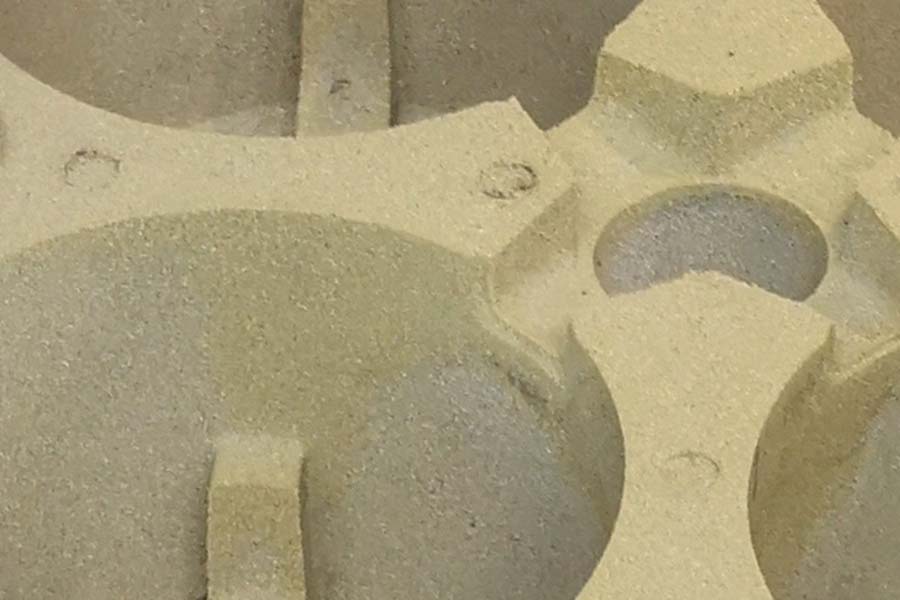
Vantagens do processo de fundição em molde de concha
1.Fundições em conchasão geralmente mais precisos dimensionalmente do que os fundidos em areia.É possível obter uma tolerância de +0,25 mm para fundidos de aço e +0.35 mm para fundidos de ferro fundido cinzento efundidos de ferro dúctilem condições normais de trabalho.No caso de moldes de casca com tolerâncias estreitas, pode-se obter na faixa de +0,03 a +0,13 mm para aplicações específicas.
2. Uma superfície mais lisa pode ser obtida em carcaças de casco.Isto é conseguido principalmente pelo grão de tamanho mais fino usado.A faixa típica de rugosidade é da ordem de 3 a 6 mícrons.
3. Ângulos de calado, que são mais baixos do que os fundição de areia, são necessários em moldes de casca.A redução dos ângulos de inclinação pode ser de 50 a 75%, o que economiza consideravelmente os custos de material e os custos de usinagem subsequentes.
4. Às vezes, núcleos especiais podem ser eliminados na moldagem em concha.Como a areia possui alta resistência, o molde pode ser projetado de forma que cavidades internas possam ser formadas diretamente com a necessidade de núcleos de casca.
5. Além disso, seções muito finas (até 0,25 mm) do tipo de cabeçote de cilindro refrigerado a ar podem ser prontamente feitas pela moldagem do casco devido à maior resistência da areia usada para moldar.
6. A permeabilidade do invólucro é alta e, portanto, não ocorrem inclusões de gás.
7. Uma quantidade muito pequena de areia deve ser usada.
8. A mecanização é facilmente possível devido ao processamento simples envolvido na moldagem do casco.
Limitações do processo de fundição de molde de concha
1. Os moldes são muito caros e, portanto, econômicos somente se usados em produção em grande escala.Em uma aplicação típica, a moldagem em concha torna-se econômica em relação à moldagem em areia se a produção necessária for superior a 15.000 peças devido ao custo mais alto do padrão.
2. O tamanho do fundido obtido por moldagem em concha é limitado.Geralmente, podem ser feitos fundidos com peso de até 200 kg, embora em menor quantidade sejam feitos fundidos com peso de até 450 kg.
3. Formas altamente complicadas não podem ser obtidas.
4. Equipamentos mais sofisticados são necessários para manusear os moldes de concha, como os necessários para padrões de metal aquecidos.
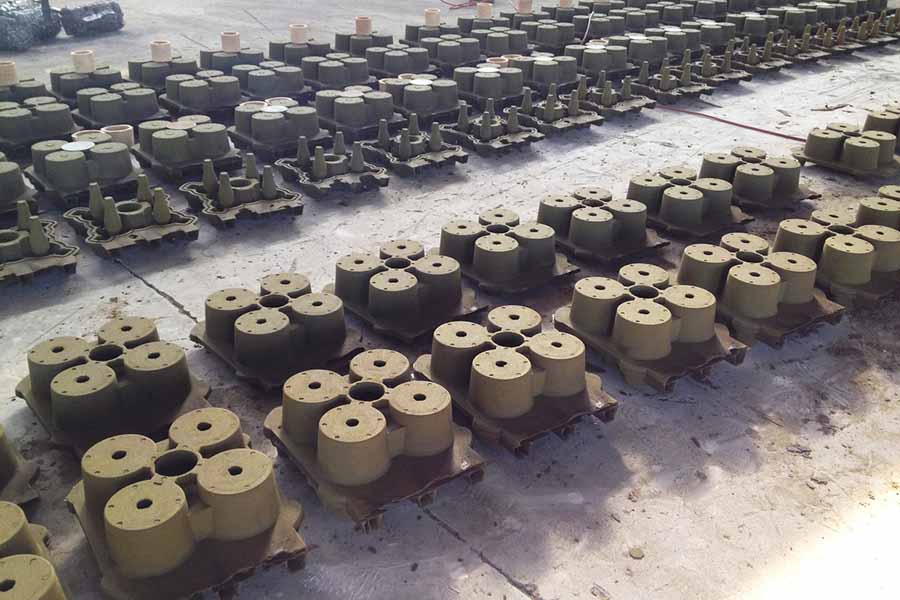
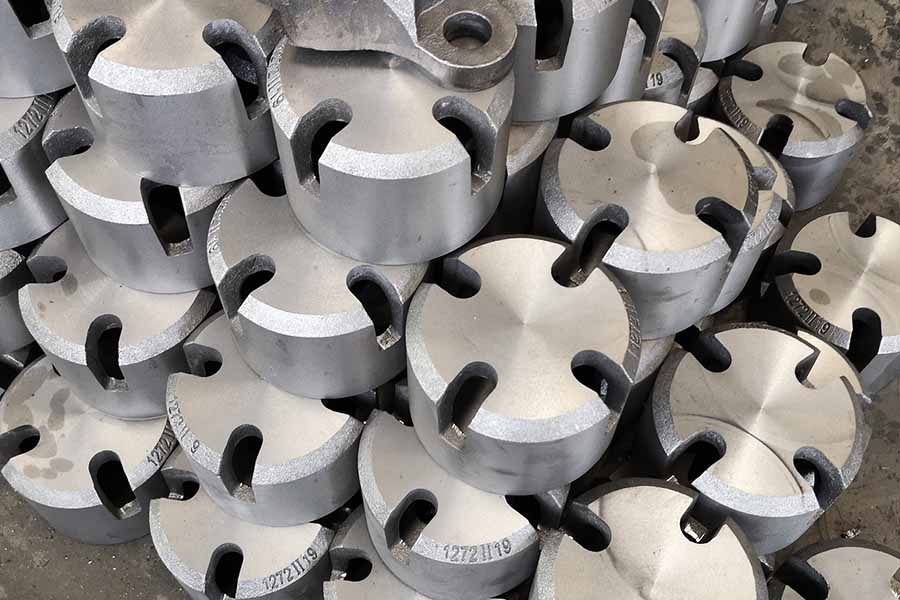
Horário da postagem: 25 de dezembro de 2020